板の製造工程
当社の大気圧を利用した真空バッグ成形法による製作プロセスを紹介します。
一般的には、CFRP板はプレス成形法が採用され、下写真・よりホットプレス機に投入し加熱・加圧し製作されます。
当社の真空バッグ成形プロセスは、工程中を通して板全面の真空引きにより、プリプレグ積層間のエアーを完全に抜くことで、ボイド・ピンホールがなく、そり・ねじれの少ない製品板を成形できます。
厚さ、平面度など高精度を要求される工業製品には好ましい製作方法と当社ではお客様に推薦しています。
今回、15t x 500W x 1500Lのハイブリッド板を2枚の製作プロセスをご紹介します。

素材(プリプレグ)は、炭素繊維を引き揃えたうえ樹脂を含ませて半硬化させたもので、硬化を防ぐため冷凍保管されていますが、写真は冷凍庫より出しパッキングフィルムを取り除いた状態です。 通常は横置きとしますが写真用に立ててあります。
室温に戻すときには、素材が結露しないようパッキングをはずす時期を考慮する必要があります。
素材の巾は1000mm、長さ100mが標準です。 厚みは豊富にあり(0.02mm~0.5mm程度まで)、作る製品に合せ選択して使い分けます。
例として10t板を作る場合は0.25mmの素材シートを40枚重ねます。
又特性の違う炭素繊維の素材を組み合わせハイブリッド(複合)成形することで性能向上・低価格を実現していきます。
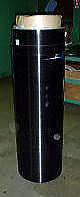

作りたい製品のサイズにカッティングします。
今回は3種の素材を使いました。
積層管理のため、カッティング時に識別表示を行います。
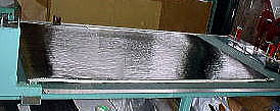

一枚ずつ保護シートをはがし、層間の空気を抜きながら積み重ねます。 このときに材料設計した素材の積み重ね順を管理しながら行います。 最も重要な工程で、出来上がり製品の良し悪しに大きな差が出ます。
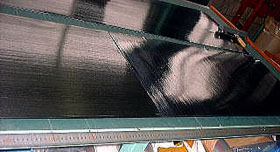

端面をそろえ3種の素材が設計どおりの順番で積み重ねられました。
プレス成形法の場合は、この時点でホットプレス機に投入し、加圧・加熱をします。
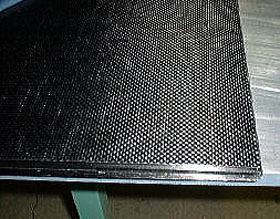

真空バッグ成形法では、ツール面の上に保護フイルムを敷き、積層された素材をセットします。
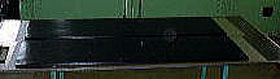

上面にも保護フイルムを敷き、その上に平滑な当て板をのせます。
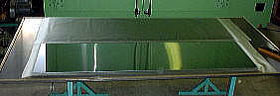

空にするためのパッケージングです。
Step3の工程で抜ききれないエアーを引き出します。(この工程が真空バッギングと呼ばれます。)
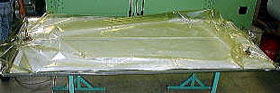

真空バッグのセッティング完了です。
少し時間をおいてリークのないことを確認します。 家庭用の布団の圧縮と同じで、大気圧がかかっています。
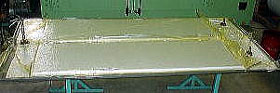

オーブン(硬化炉)に投入です。
バキュームホースがつながっていますが、真空引きはオーブンが冷えるまで行います。 今回は130℃で2時間加熱します。
使う素材(樹脂の種類や、素材の積層厚さなど)により加熱温度プロファイルは異なります。
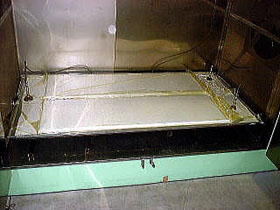

完全に冷えた後オーブンより取り出し、パッケージをはずして完成です。 この後、成形板の耳をトリミングします。
マシニングセンター等の機械加工機で、切削や研磨などの研削加工ができます。
加工内容により、ソリやネジレの発生については確認する必要があります。 特に、ハイブリッド成形板の場合は要注意です。
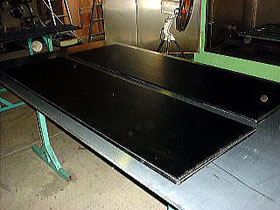